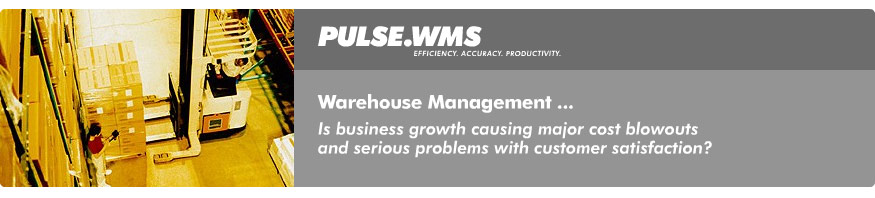
PULSE Warehouse Space Optimisation
Despite this though, it often seems that the warehouse is not required to justify itself to the same extent as other assets. And while all of the things that actually go on within its walls are typically the subject of corporate scrutiny, and the target for improvement, not so the warehouse itself.
So on the one hand, we find increasing levels of attention being paid to raising staff productivity, to reducing stock levels, to minimising error rates and the like. And rightly so. But on the other hand, it’s far less common to find organisations paying special heed to the analysis of ‘warehouse utilisation factors’. The extent to which each storage location of expensive space is contributing to the business. The return that it is giving on its investment. How effectively it is now being used. How its use could be substantially improved.
Nor is this at all hard to explain.
It’s simply that the traditional procedures in place in most warehouse operations have provided very little in terms of practical and useful space management techniques. And without sound methods to help improve and fine tune utilisation, its existing status has tended to be regarded as a fait accompli. Something that basically has to be lived with, certainly as far as the short and medium terms are concerned.
Now with the PULSE Warehouse Management System (WMS), things are at last very different. For in providing all of the necessary tools appropriate to the optimisation of operations, PULSE goes on to deliver some very major utilisation results.
Results which wide user experience demonstrates can reduce warehouse space requirements by 10–30 per cent and which have been translated into the ability to:
- Cater for solid business growth without added warehouse capacity
- Take on more products/suppliers with current storage resources
- Consolidate multiple warehouse sites
- Hire out excess space
- Greatly extend contract services within existing building confines
The Total Space Equation
Such potential savings are doubly significant, given the very broad (and indeed logical) definition of ‘space’ that PULSE applies to its space optimisation duties.
So that while it most certainly begins by considering overall warehouse structures, in basic building bricks and mortar terms, it then goes on to extend its thinking much further. So it adds to the overall equation any of the racking, handling equipment and specialised devices that are necessary to convert such premises into a working operation. Those fitting out assets that are high on cost and which, if not properly managed, quickly become a major component of the optimisation problem as opposed to being part of its solution.
In other words, the PULSE WMS equation is all about the total costs of ‘space’, and the management and optimisation of all of the component parts that are included. It is as concerned about equipment that is only having part of its capacity used because of inefficient warehouse layout, as it is with that layout itself. And the efficiencies it helps introduce are as equally focused on minimising the need for additional materials handling devices as they are on removing the need for new building capacity.
Flexibility
Just as PULSE’s view of warehouse space is a broad one, so too is it highly flexible. Thus the type of facilities using the system can be those where shelving or block stacking or racking is involved. They may be those where controlled temperature storage is all important, or where specialised 3PL contract services are the nature of the business.
Or they may be those called upon to provide the additional capabilities uniquely demanded by such things as stock rotation, and ‘use by’ date or batch/lot number control requirements. In these and all like cases (and indeed with all combinations) the space management techniques of PULSE are equally applicable and powerful.
Likewise at the product level, where optimisation can be achieved with any kind of stock dimension, weight, or shape, including uglies. Indeed as we regularly note, such is the flexibility of PULSE that its current application is to products as diverse as: smallgoods, books, seafood, uniforms and fruit; office equipment, furniture and chocolates; PCBs, hospital supplies and poultry; machine parts, beverages, pharmaceuticals and pastry; vegetables, jams, canned foods, stationery and telecommunications equipment.
Space Management Techniques
At the heart of PULSE warehouse optimisation are the space management techniques that form an integral part of its design and day to day operations.
Techniques which are in turn based on two fundamental characteristics of the system. These:
- Define the overall facility in terms of each and every one of its discrete storage locations. All space is thus specifically managed on a location by location basis.
- Control all individual stock movements under on line and real time computer procedures. At any moment, therefore, any particular stock keeping unit (SKU) can be precisely located. And equally, the present storage status of any holding area is always known exactly.
Given such a starting point, warehouse management may at last begin to think about product storage and movement in a number of significant new ways — each contributing to operational efficiency and effectiveness, and to space savings.
Consider.
To coincide with its installation of PULSE, the warehouse can use industry standard ABC analysis of its historical data to appropriately identify fast, medium and slow moving stock items. (Subsequently, PULSE transaction summaries provide the ongoing data to continuously fine tune such reviews).
Based on this information, locations can then be allocated to give the most efficient holding and retrieval layout possible. Slow stock can be placed in the least accessible parts of the warehouse. Its most convenient and central areas can be dedicated to fast moving items. While such allocations may also specify multiple products per location and multiple locations per product.
Most importantly, PULSE’s total location management also enables all of this to be done on a ‘group’ basis. So, for example, all (or groups of) fast moving SKUs can be collectively allocated to all (or groups of) optimum storage locations. Among other things, this ‘random’ allocation capability means that no longer do individual stock items have to be assigned to specific, rigid and predetermined locations. The more traditional method of ‘fixed’ allocation that results in some space sitting empty for extended periods while other locations are bulging at the seams.
Additionally, it’s also a straightforward matter to spread high turnover items thought the areas designated to them. This to ensure that a number of simultaneous transactions do not create bottlenecks amongst the operators on the warehouse floor. And again such a capability being feasible because of the precise location management which is in place.
What then precisely happens when the putaway of new stock is called for? Here PULSE will automatically determine the ‘best fit’ location possible for the product based on the predetermined set of rules specified by the user. Such allocation will consider all of the designated space that is available, its present storage status, the equipment needed to access it and that which is available, and all other current and pending transactions that are relevant.
Similarly with picking. Having been told what product and what quantities are required, PULSE again determines what are currently the optimum locations from which to extract the stock in question. This will automatically review other related pick or putaway activity that is currently scheduled for the item and pick face in question. And it fully takes into account any ‘use by’ date, FIFO, serial number, or batch/lot number control considerations that have been nominated.
Lower Inventory Levels
But such space management techniques are by no means the only way in which PULSE enhances warehouse utilisation.
Take, for instance, its capacity to reduce inventory levels by 15 per cent or more. Such a capability is well proven and documented, and spans a diverse range of industries. And is presented in some detail in the further PULSE product sheet ‘Inventory Savings — Economy in Tune with Efficiency’.
This notes that from the time of initial goods receipt to the point of final despatch, deficiencies in each and every step of the overall warehouse process can force the need for stock levels that are far in excess of those really needed. Excesses which, when the cumulative effects of such problems are taken into account, typically equate to 15 per cent or more of optimum stock levels.
Conversely, PULSE is designed to overcome these traditional shortcomings, and does so throughout the entire warehouse cycle. From receivals and putaway. Through replenishment and picking.
To order assembly and despatch. In each instance, less stock clearly and immediately translates into reduced warehouse space requirements.
Productivity
A great deal of time in many warehouse operations is quite simply wasted. That is not to say that people and equipment are not busy. It’s just that these resources have to focus so much of their efforts on work that should not need to be done in the first place.
The list of such unproductive duties is extensive. It includes all of the time that is spent looking for things. Shifting items around unnecessarily. Downtime while lots of paperwork is handled. Trying to locate long gone items that the system alleges are still there. Making repeat trips to one location, when one would have sufficed. And so on.
With the strategy provided by PULSE, productivity wastage can be largely removed because its causes are removed. And such are the benefits that this can provide that typical user experience shows a 30 per cent plus saving in resource costs.
Such resources quite obviously have a significant personnel element. However it is the equally major savings in materials handling devices and equipment that result which further add to overall ‘space’ optimisation.
The Management Dimension
The WMS tools that contribute to this more efficient use of present warehouse ‘space’ also combine to provide potent warehouse utilisation data for management. Analysis that is now able to look at the financial contribution of each and every warehouse location. And which can be used to critically examine the longer term role, capacity and function of the warehouse as part of the overall organisation.
So alongside maximising existing resources and minimising the need for future building and equipment expansion, PULSE delivers the mechanisms to put warehouse ‘space’ under the same level of scrutiny as other key corporate assets.