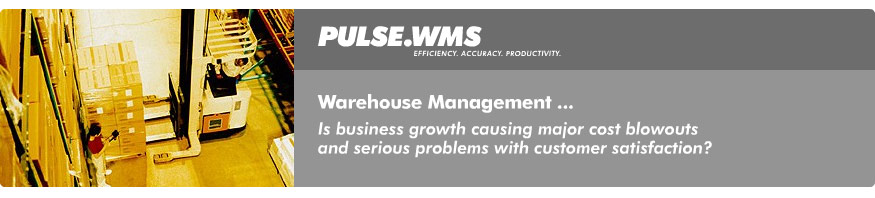
PULSE Productivity
With the advanced warehouse management strategy provided by PULSE, productivity wastage can be largely removed because its causes are removed. And such are the benefits that this can provide, that typical user experience shows a 30 per cent plus saving in resource costs.
In day to day operational terms, such productivity gains are achieved by the potent combination of automatic work allocation and vastly improved accuracy. They are further enhanced by enabling management to focus on exceptions rather than the norm, and to oversee a program of continuous improvement within the warehouse function.
Automatic Work Allocation
In a great many warehouses, real life does indeed approximate to the standard 80:20 rule, with the bulk of individual transactions being relatively routine.
For all such routine instances, the user is able to define for PULSE all of the ‘rules’ that need to apply to each and every product movement into, within and out of the warehouse. Rules that may be regularly reviewed and updated, and which include:
- Qualifications of all operators
- Restrictions and capacity of materials handling equipment
- The type of work each person and item equipment is able to do • Full location control data including volume and weight holding capacity details, movement class control and storage type specification
- Best ‘use of available space’ criteria
- Definitions of required stock rotation and ‘use by’ date parameters etc
- Pick face replenishment criteria
With such a database of information in place, automatic work allocation can then be readily achieved.
All relevant work to be done is appropriately scheduled by reference to the rules and with all needed resources being calculated.
Whenever free, operators and equipment ‘call for work’. Work to be done and free resources are automatically matched and specific duties assigned.
Such duties can include multi pick, wave or bulk picking etc and the subsequent tasks of order consolidation or pick breakdown.
In this manner PULSE proactively schedules the activities of equipment and people to help ensure that more productive work can be carried out in much less time.
Improved Accuracy
But of course, for such scheduling to be truly effective, the information on which it is based must be fully accurate. And accuracy in this context means not only error free but also totally up to date — two necessary qualities to which PULSE is singularly well attuned.
Its capacity to eliminate warehouse errors, for example, and the means via which this is achieved, are absolutely central to the system’s design. These are described in detail in a separate fact sheet. However, in summary, it is noted that with PULSE, user experience shows that error rates can be consistently reduced to 0.1 per cent or less. This results from integrating into the PULSE system a range of modern tools and proven procedures. Facilities such as individual item tracking; barcoding for easy product and location identification; cross checking and monitoring and ‘real time’ processing and updating using data transmission via radio (RF) terminals.
In terms of productivity improvements, the absence of errors means the elimination of such things as:
- The vast array of rehandling processes that are associated with accepting back incorrectly shipped orders
- The function of repicking and reshipping replacements for such incorrect orders
- Staff and equipment being sent to incorrect stock locations
- Or to locations in which the incorrect stock has been placed
- Or to locations in which there is presently insufficient stock
- Lengthy, time consuming and costly stocktakes
- Delays resulting from incorrect product characteristics being recorded (batch numbers, lot numbers, ‘use by’ dates etc)
- The matching of products to unsuitable locations (size, weight, temperature control, etc)
The same system building blocks of PULSE also guarantee that all critical information affecting the warehouse’s operation is up to date. For instance, whenever an item of stock is moved, RF terminals are used to immediately update the central system. Consequently this always shows where an item is now rather than where it was supposed to be some time ago. Where it was, perhaps before a whole lot of other picking orders for it were actioned and before some replenishment was initiated. Translated into specific productivity savings this prevents the occurrence of many traditional time wasting scenarios such as those where:
- Large amounts of time are spent simply looking for stock
- Staff are regularly assigned duties that cannot be performed
- The lack of up to date information means workflow cannot be effectively scheduled and controlled
- Replenishment work is initiated to cover orders that have yet to be picked
- Picking work is delayed because the completion of replenishment work has yet to be reported
- Multiple order picking cannot be effectively pursued because of the inherent problems associated with each individual picking requirement
- Efficiency is compromised by low staff morale. This resulting from the need to continually repeat work because of system deficiencies
Management Productivity
Just as PULSE will streamline the bulk of general activities, so too will it help free up considerable amounts of invaluable management time. Time that will no longer be needed to attend to day to day routine operations. And instead can be focused on the critical exceptions.
Most importantly in this context, what are and what are not to be treated as ‘routine’ are totally user defined. So that in addition to those more universal situations that will always demand attention, quite specific options can be added. It could be decided, to cite but two examples, that any transactions to do with new customers or new products would be flagged so that additional supervision could be invested.
No matter what the criteria however, PULSE identifies all such exceptions and immediately highlights these in pertinent management action alerts that are provided in video terminal and hard copy format. So such things as problem situations are precisely advised on. Advised as and when they occur. When some form of corrective action can at once be initiated. And not some hours, days or even weeks after the event.
Relevant summaries highlighting current bottlenecks and inefficiencies can also be generated, so that a program of continuous improvement can be added to the already forceful productivity equation.
The Clerical Dimension
Last but certainly not least are the invaluable productivity gains that are achieved in clerical and associated operations. Vast volumes of paperwork quite simply become a thing of the past, as does the bulk of the time consuming, and usually repetitive, data entry activities that have to service traditional operations.
Aside from dispensing with the sheer workloads that such clerical overheads demand, the errors that unavoidably accompany them are removed. These productivity gains consequently have a multiplier effect as the time and effort needed to correct mistakes is avoided.