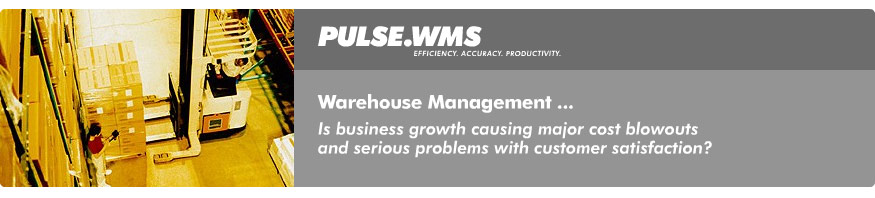
PULSE Inventory Savings
In practise, this is achieved by linking to advanced hardware and software tools fully integrated barcoding and data transmission via radio (RF) terminal technologies.
Barcoding is used to uniquely label every warehouse location and all goods from time of receipt through to despatch. This ensures that every stock movement can be automatically checked to ensure its validity and accuracy.
Aside from its other benefits, RF equipment contributes to such processes by ensuring that all relevant warehouse date is always totally up to date. So at any time the system knows precisely what volume of what stock is in what location.
The practical day to day benefits this provides is most starkly presented by considering the harsh realities of a warehouse that does not use WMS and remains driven by ‘after the event’ batch processing and excesses of paper.
The Batch/Paper Chase
In such a traditional approach, the inordinate volume of paperwork that is generated is enormous, all of it contributing to substantial bottlenecks. Bottlenecks that can quite clearly be identified:
- At receivals and putaway
- During replenishment and picking
- At order assembly and despatch
Consider:
Receivals
As goods arrive at the receival dock, delivery documents are handed over to the receivals clerk. The paper work is verified against any outstanding purchase orders for that supplier and the newly received stock is accepted into inventory. Of course, even at this early stage, considerable delays can occur. The document searching and matching process can often take considerable time even if things are totally correct. If they are not, then an even greater lag occurs. And all the while inbound products are sitting idly.
Certainly at this stage the stock is eventually recognised as inventory. Even then, however, it may not necessarily be made available for picking until the system has received advice that the products have in fact been placed into a location.
In other words, there is stock that is effectively in limbo. It exists, the system knows it is there, but nothing can be done with it apart from producing a piece of paper instructing an operator to take it to a location.
In fairness there are some paper systems that will commence to process information in relation to back orders that may exist for the newly received products. They may even create a paper movement transaction to have the product taken straight to an order assembly area. But this of course does nothing for the balance of that stock.
Putaway
Having successfully received stock, the batch/paper system will typically then go on to produce putaway instructions. This paperwork will be duly handed out to an operator who in turn carries out the manual task of collecting the stock and delivering it to the location indicated.
It is not uncommon for the operator to collect a number of putaway instructions and clear a number of pallets before handing back the confirmation of the transaction. The critical elapsed time here varying from 15 minutes to several hours.
The reasons for this delay are many and varied. For example, the operator may arrive at the specified location to find that there is product already there. Or it may be a particularly complex receival that has numerous ‘use by’ dates or batch numbers that all need to be recorded. It may in fact be a combination of events and mistakes that takes a transaction (which on the face of things appears to be a relatively simple and straightforward task) and turns it into an enormous waste of precious time.
The Story So Far
So to this point we have already identified the receival dock and transit to putaway as two areas where either stock exists but is unavailable, or where it might even be unknown to the warehouse’s traditional system.
In environments where service levels are measured in terms of orders fulfilled against available stock, it is not unheard of for the more innovative of staff to inflate their performance by simply delaying the updating of their systems. A costly example of lateral thinking essentially encouraged by a traditional paper approach.
Replenishment and Picking
In most batch/paper systems, replenishments are triggered by the ‘assumed’ stock in a picking location falling below a predetermined point. Which appears to be a perfectly reasonable approach, until the mechanics of such a process are examined.
The key lies in the manner in which the picking slips are produced and for which two fundamental options exist:
- Picking slips are produced in a batch and the total stock of all the items on those pick slips is calculated. If those totals then place one or more of those items at or below their preset replenishment point then replenishment instructions will automatically be produced. All of this happens before the pick operators have even collected their picking slips. As a consequence, the replenishment stock arrives at the pick location before the stock it is meant to replace has been picked. Finding no room in the pick location, the conscientious replenishment operator will then return the stock to the location from whence it came.
- Alternatively, replenishments are not activated until picking slips have been completed and acquitted back into the system. While these pick slips are in process or are being confirmed, other pick slips will have been generated. These transactions occur on the assumption that the necessary replenishments have taken place.
In these circumstances the replenishment stock arrives at the pick location too late for the next set of pick slips.
In either instance, the net effect is:
- Wasted time in moving product
- Secondary pick runs to select stock
- Pick slot inventories that need to be set at inflated levels
Order Assembly and Despatch
With batch/paper systems, it is not uncommon to find that significant quantities of stock are somewhat arbitrarily ‘reserved’ by management and supervisors to provide a kind of operational insurance policy. In such instances product is removed from stock and is held in a number of completed or partially completed orders quite some time before this work actually need take place. The decision to do this might simply be to ‘get ahead’ while an opportunity presents itself. It may be done to ensure that upcoming key transactions, such as those for major customers or for export orders, can be quickly and fully met when the time comes. Or it may be in response to large and known regular orders where it is imagined that anticipation of workloads will contribute to efficiency.
In all such instances, the intent of this allocate and reserve policy may be commendable. With a batch/paper system it may also be unavoidable. However the obvious downside of the equation is that short term, day to day requirements for the same product lines will then only be able to be filled via additional work and if extra stock volumes are held. This despite the fact that all orders could have been fully met with the original stock levels had unnecessary reserving not occurred.
Like all other functions within the manufacturing and distribution cycles, assembly should be carried out ‘Just In Time’. However with batch/paper systems’ inefficiencies, error rates, long lead times and replenishment uncertainties, this remains an unachievable impracticality.
The Overall Picture
In essence then, from the time of initial goods receipt to the point of final despatch, deficiencies in each and every step of the overall warehousing process can force the need for inventories that are far in excess of those really needed. Excesses that, when the cumulative effects of such problems are taken into account, can typically equate to 15 per cent or more of optimum inventory levels. And it is for these reasons that one of the fundamental design and implementation objectives of PULSE is to deliver a system to users that will directly overcome these traditional shortcomings. The end result is a proven approach that over a very short period of time will enable stock levels to be paired back to those optimum volumes.