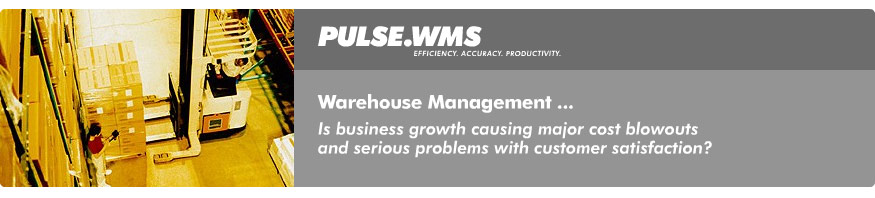
PULSE Error Reduction
|
But even without such loadings, error overheads impact profit alarmingly.
As worrying as the cost of individual mistakes is, so too is their frequency.
Here further studies suggest that typical error rates are between 3 and 5 per cent. Even firms achieving the lower rates often fail to do so consistently, particularly at pressure points such as month ends.
It is also a fact of life that all too frequently problems grow when they are singularly least appropriate. New marketing thrusts, new product introductions, and new customers will all generate more warehouse workload, where errors can totally negate the investment that’s been made to win new business.
When combined, the arithmetic of such harsh figures shows that with a 3 per cent error rate, a base error cost of just $75 and (say) 5000 transactions per month, then what is being talked about is a monthly cost of mistakes of $11,250. And that just for the privilege of getting things wrong.Reducing Error Rates to 0.1 Per Cent or Less
Some human error is, of course, unavoidable. However, when the sorts of rates that have just been noted are observed, much of the blame must be placed on the systems that are in operation.
Of great importance, and great comfort, is that these latter problems can now be overcome.
With PULSE, user experience shows that it is possible to consistently achieve 99.9 per cent or better accuracy. This is achieved by integrating into the Warehouse Management System a range of modern tools and proven procedures.
Facilities such as individual item tracking; barcoding for easy product and location identification, cross checking and monitoring; and ‘real time’ processing and updating using data transmission via radio (RF) terminals. Facilities which when effectively combined, make 0.1 per cent error rates or less a demonstrable reality.
The Path to Error Avoidance
In practise, such a reduction in mistakes is achieved via a combination of approaches.
In picking alone these ensure:
- The absolute accuracy of location details
- The specific accuracy of stock levels in each location
- The accuracy of pick
- Totally up to date information that guarantees the warehouse is operating on current data, not best guessed historical information
- That priorities are automatically handled, so picks can be actioned when they need to be
- The elimination of paperwork and its inherent transcription and interpretation errors
- The automatic control of such things as stock ‘used by’ dates (which can also be automatically matched to individual customer acceptance and discounts for varying expiry lead times)
- The similar control and consolidation of product batch or lot numbers on a customer by customer basis
- Serial number control
But of course, picking is but one part of the overall warehouse cycle where errors can regularly occur. And given the absolute logic of getting it ‘right from the start’, the effective control of the receiving process is a further area in which PULSE makes a valuable contribution. Here avoiding errors is facilitated via the:
- Automatic checking against purchase orders, EDI/Web reports or factory release data etc, that what has arrived is exactly what was expected
- Immediate recording of any discrepancies so identified, and the initiation of follow up supplier action as defined by the user
- System’s generation of receiving label barcodes (in addition to supplier’s own or where these are absent) so that precise product identification can continue to be made
- Automatic assignment of goods to their immediate point of holding, eg inspection, quarantine, pick location, reserve stock
Under this latter process, the system decides to where a particular item should be directed under user defined parameters. The putaway is then assigned by PULSE to the most appropriate warehouse operator/equipment combination. In so doing:
- The operator will scan stock to be moved to ensure that the correct items are about to be handled. Errors are immediately trapped
- Once at the putaway location, this is scanned to ensure it too is correct. Again any mistakes are immediately averted
- Putaway paperwork and its unavoidable transcription errors are eliminated. So too are any delays in updating stock location records that would cause subsequent picking problems
At the other end of the entire warehouse operation, contributions to accuracy are equally present.
Thus: - Where wave or bulk picking has been used to generate efficiency and productivity, PULSE provides the further controls needed to carry out subsequent splits into individual orders. This without the need for extra staff or the risk of error
- Where an order has been split picked, automatic control monitors when it has been fully and correctly completed
- PULSE further controls the assembly of individual orders in terms of such things as warehouse grid and delivery run numbers. Barcoding checks again ensure things go where they are supposed to, and conversely that nothing is accidentally placed where it should not be
- Error control right down to the individual shipment is provided by the generation of load and delivery details to assist with ‘proof of delivery’
- And if required, such data can be made available for subsequent checking against transport company invoices, to help protect against other people’s errors
The Avoidable Cost of Errors
Potential Costs Associated with Despatch of Incorrect Orders
Basic costs of :
- Return Transport
- Re Receiving Procedure
- Inspection on Return
- Quarantine on Return
- Damaged Goods Procedure
- Damaged Goods Write Off
- Re Packaging
- Re Putaway
- Additional Data Entry
- Credit Note Procedures
Costs of (Correct) Replacement Order
- Re Picking
- Re Packing
- Re Transportation
- New Documentation
Intangible Costs
- Lost Business Sales
- Staff Effort
- Compromised Customer
- Management Effort
- Satisfaction
Situation Specific
- Export Transport Costs
- Customs Penalties for incorrect Paperwork
- Perishable Goods Spoilage
- Contract Penalties
Other Potential Business Costs
- Loss of Repeat Business
- Loss of Customer Service Reputation
- Staff Dissatisfaction and Turnover
- Reduced Ability to Attract Best Staff
- Inability to Achieve Quality Standards Accreditation
